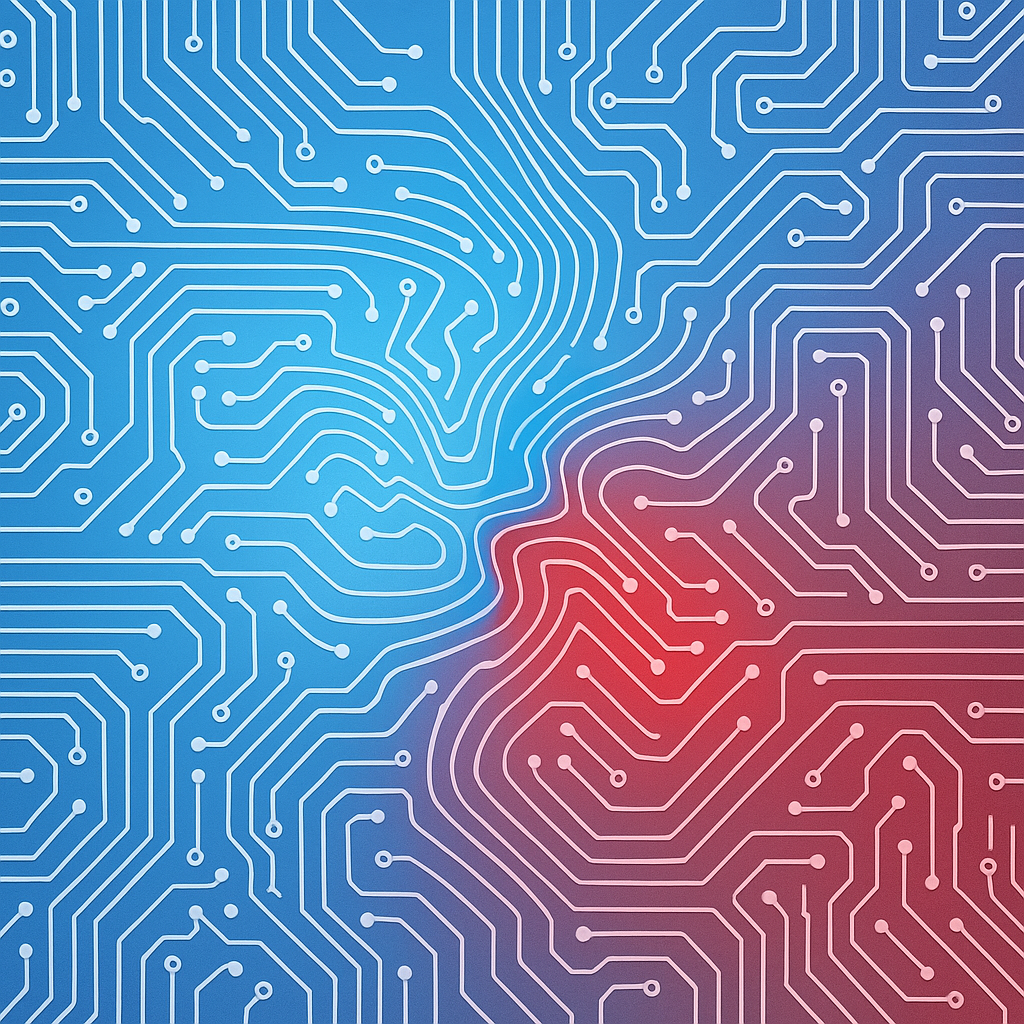
I. Introduction: Calibration as an Energy Principle
In engineered systems, calibration is the process by which instruments, devices, or components are adjusted or verified to produce accurate, repeatable results in response to known, controlled inputs. It is foundational to functional accuracy, safety, and operational consistency. Whether in electrical circuits, materials testing, or sensor arrays, calibration ensures that the system interprets and responds to energy in a way that matches its design expectations. At its core, calibration involves establishing a reliable relationship between an input signal (e.g., voltage, pressure, electromagnetic wave) and an output response (e.g., meter reading, signal amplitude, or material deformation). This relationship must remain within a known tolerance band across the operating range of the system. In practical terms, a calibrated system behaves predictably under defined conditions, enabling engineers and operators to trust the data and responses it produces. This principle applies not only to isolated instruments but to broader interconnected systems. From sensor networks and automated diagnostics to entire control systems in energy grids or aerospace environments, calibration underpins systemic reliability. The same holds true in biological ecosystems and even in organizational or cybernetic systems, where response fidelity depends on the alignment of internal and external parameters.
Three foundational performance attributes define a calibrated system:
- Linearity: the system’s output changes proportionally to changes in input.
- Sensitivity: the system can detect and respond to small variations in energy.
- Uniformity: the system provides consistent responses across different zones or input paths.
However, recalibration is not always possible – and not always successful – especially when systems experience long-term exposure to incompatible inputs, structural degradation, or environmental overload. Resilience, internal coherence, and historical alignment patterns play a critical role in whether a system can be recalibrated after deviation. Simply applying calibration procedures does not guarantee realignment, particularly in systems with deep-set impedance mismatches or corrupted feedback pathways. A wide array of tools is used in professional and industrial calibration workflows. Each is designed for specific material properties, energy types, and measurement domains:
- Radiodetector: subsurface imaging based on reflected radar pulses.
- Ultrasonic Pulse Velocity (UPV): Measures the speed of sound through solid media to infer integrity.
- Oscilloscopes and Signal Analyzers: Visualize waveform behaviors to identify timing or amplitude anomalies.
- Spectrum Analyzers: Assess frequency domain characteristics of electrical signals.
- Rebound Hammer / Hardness Testers: Evaluate surface hardness as a proxy for material strength.
- Multimeters and Power Quality Analyzers: Assess voltage, current, and frequency behaviors in circuits.
These instruments enable the detection of drift, degradation, and anomalies – but they operate only within known, compatible frequency and material profiles. Calibration tools are not correction tools. They do not convert or harmonize incompatible inputs; they only measure deviation and report failure to align. Ultimately, calibration operates within a domain of compatibility. When input/output structures diverge beyond defined tolerance – whether due to signal type, waveform behavior, or structural mismatch – calibration becomes not just difficult, but physically impossible. This is where systems reach their re-alignment limits, and where more profound phenomena such as impedance mismatch and energetic rejection begin to emerge, which will be discussed in this article.
II. Calibration Dependencies and Blocking Conditions
II.a. What Calibration Relies On
Calibration, whether applied to physical systems, diagnostic instruments, or energy models, is not a standalone operation – it is contingent upon a series of foundational dependencies. A system cannot be calibrated in isolation; it must be structurally capable of receiving, interpreting, and responding to corrective input. This requires internal integrity, environmental consistency, and stable informational pathways.
- Internal Coherence
A calibrated system assumes internal synchronization – where its subsystems communicate without delay, distortion, or contradiction. In a physical structure, this may refer to consistent material density or stable geometry. In more complex systems, it reflects biochemical readiness, timing accuracy, or computational clarity. Without coherence, calibration attempts yield misleading results or fail altogether. - Environmental Signals
Calibration is highly sensitive to environmental input. Systems interacting with ambient electromagnetic fields, temperature gradients, or mechanical vibration must account for these external variables. A system exposed to fluctuating environmental noise cannot maintain stable baseline readings, and recalibration in such a setting becomes error-prone or impossible. - Informational Alignment
Signal-to-noise ratio matters – not just in electronics, but in data-driven systems. If the system ingests high volumes of corrupted or irrelevant data, it loses the ability to distinguish between signal and distortion. In calibration terms, this blocks meaningful adjustments. Truth-filtering mechanisms – whether physical, digital, or logical – are essential to isolate actionable input from background noise. - System Linearity
Linearity refers to a system’s ability to produce output in proportion to input. Calibration depends on this predictability. Non-linear systems – such as materials exhibiting hysteresis or systems with chaotic feedback loops – require additional modeling before calibration can even begin. A distorted response curve prevents accurate baseline establishment, resulting in imprecise or misleading corrections. - Uniformity of Response
Calibrated systems must respond consistently across their operational range. If different regions or modules of a system exhibit unequal sensitivity or behavior (due to wear, damage, or design flaws), the calibration becomes localized and cannot be generalized. In composite systems, non-uniformity causes misalignment between subsystems, degrading overall coherence. - Energy Type Specificity
Different forms of energy – electromagnetic, thermal, acoustic, nuclear – require corresponding calibration models and instrumentation. You cannot calibrate an X-ray detector using radio signals, nor apply thermal calibration logic to microwave systems. Input energy must match the detection profile. Cross-type calibration attempts result in rejection, distortion, or null response. - Spectral Anchors and Reference Standards
No calibration can be performed without reference to a known, stable benchmark. In electronics, this might be a standard frequency source. In spectroscopy, it may involve elemental emission lines. These references provide spectral anchors – precise energy levels that allow for drift correction and alignment. Without such standards, calibration lacks grounding. - Multiyear and Temporal Data
In simulations and real-world energy systems, short-term data provides insufficient calibration confidence. Longitudinal patterns; stretching across months or years; reveal deep drift, latent anomalies, or structural wear. Systems with long histories of misalignment may require iterative recalibration efforts or even a complete systems reset. One-off calibration interventions are insufficient when foundational deviation has accumulated over time.
II.b. Recalibration Blocks: What Instantly Disrupts or Prevents It
Despite optimized procedures and calibration tools, certain conditions lead to immediate calibration failure. These are not subtle performance degradations – they are structural blocks that arrest the recalibration process entirely.
- Signal Distortion
When incoming signals are corrupted – whether by misinformation, degraded analog input, or spurious harmonics – the system cannot distinguish genuine reference points. Calibration performed under distortion leads to erroneous baselines, misconfigured responses, or systemic failure. - Non-linearity Beyond Repair
Once a system crosses a certain threshold of non-linearity, recalibration becomes mathematically unstable. Feedback loops may introduce exponential deviation or unpredictable phase shifts, rendering the system unfit for tuning. - Incompatible Energy Types
Calibration assumes energy compatibility. When systems are exposed to foreign or incompatible input types – such as digital waveforms forced into analog receivers – the result is not adaptation but rejection or damage. No tool can resolve incompatibility at the source level. - No Stable Reference Point
Calibration cannot be performed in the absence of a verified reference. If the system lacks a known zero-point, anchor frequency, or stable source, any attempt to recalibrate will float against uncertainty, introducing compounding errors. - Energetic Overload or Contamination
When a system is exposed to signal flooding, high EMF environments, or persistent noise, its internal components saturate. This overload inhibits responsive adjustment and introduces latency, heating, or random fluctuations that corrupt calibration attempts.
Calibration Factors vs. Disruption Sources (3 x 3 matrix):
Calibration Factor | Disruption Source | Effect
Linearity | Chaotic feedback | Distorted response curve
Uniformity | Contamination, wear | Fragmented calibration
Energy Type | Incompatible input signal | Null or dangerous output
III. False Calibration: When Conversion Fakes Energy Alignment
With the prerequisites for calibration now defined, it becomes critical to examine what happens when those foundational conditions are absent; when calibration is attempted, but fails due to structural incompatibility. This is where the concept of false calibration emerges: a scenario where superficial adjustments give the appearance of realignment, but no true energy transfer or system resonance is achieved. In technical systems, calibration is a precision-dependent process. When integrity within the system drops below a functional threshold; due to structural incompatibility, recalibration cannot proceed. Attempting to “force” recalibration in such conditions produces illusions of alignment, not true correction.
This failure mode can be captured under a hard truth: There is no middleware for energetic misalignment. Compatibility is not optional – it is structural. Some systems or external agents may respond to persistent mismatch by attempting a complete teardown – dismantling the original system architecture in hopes of rebuilding something more compliant. But even this fails when the core frequency or structural identity is not programmable or replaceable. Demolition does not equal transformation.
The frequency encoded into the original system is not a surface property; it is foundational. Rebuilding it does not rewrite it.
- The Output May Adjust, But the Core Frequency Does Not Change
In situations of false calibration, a system may be forced to produce expected outputs – much like a misconfigured sensor temporarily showing readings within an acceptable range. But if the internal frequency, architecture, or material profile is not aligned with the input signal, those outputs are non-resonant artifacts, not indicators of true function. The external observer may see compliance – a system behaving “as if” it were calibrated – but internally, there is no synchronization. The core frequency remains unchanged. This is equivalent to simulated alignment, where outward responses are curated or coerced to match expectations, while internal systems remain out of phase. Over time, this creates cumulative stress, signal degradation, and eventual breakdown. - Energetic Misuse Feeds Distortion, Not Power
An illustrative example is found when a system attempts to extract energy from an incompatible source – particularly when the source has not consented to or aligned with the transfer. In energetic terms, this is not power – it’s distortion. The initiating system receives only surface-level echoes, not core signal. These echoes are inherently unstable, lacking continuity or feedback reinforcement. What results is a feedback loop filled with interference, depletion, and systemic fatigue. The source becomes drained; the receiver becomes unstable. Nothing meaningful is transferred. It is the energetic equivalent of extracting noise from a silent channel and mistaking it for signal. - You Cannot Convert What Was Never Compatible
In engineering, AC and DC circuits cannot be directly connected without a converter. Even with converters, the transformation is not seamless – it’s a forced shift that requires specialized infrastructure. Without it, attempting a direct connection causes sparking, damage, or system failure.
The same applies in calibration and system design. Core frequency, material architecture, and signal identity must align structurally. No converter exists to rewrite that identity in a way that produces functional compatibility. If two systems were never designed to resonate together – or if their design principles contradict – any effort to create calibration will yield only friction or feedback rejection. Even if visual or surface adjustments are made – language changes, gestures mirrored, interfaces tweaked – the lack of core resonance means no true fusion occurs. This leads to False Calibration Leaves a Distinct Signature:
Fragmented feedback loops
A loss of internal system coherence
Energetic mimicry: Output generated through coercion or adaptation, not true response.
Performance under pressure: Apparent functionality sustained through stress or imposed expectation.
Output without resonance: Energy that fails to connect, nourish, or return.
Mimicked behavior under pressure. In practical terms, this is a counterfeit calibration loop – it may look operational, but underneath, it is hollow. Ultimately, nothing sustainable is built from such a configuration. False calibration is not just inefficient – it is destructive over time, introducing wear, stress, and brittleness that degrades both systems involved. What appears on the surface as successful calibration may, in fact, be the earliest sign of long-term system failure.
IV. Calibration Failure and the Bounce-Back Effect of Impedance Mismatch
Impedance Mismatch: When Calibration Fails by Design
In engineered systems, impedance is a fundamental property that governs how energy flows between components. It encompasses not just resistance (in DC circuits) but also the combined effects of capacitance and inductance in AC or RF systems. When two systems or components interact, successful energy transfer requires that their impedances be closely matched. If this condition is not met, the result is impedance mismatch – and it marks the precise point at which calibration ceases to function. Impedance mismatch occurs when the load impedance differs significantly from the source or transmission line impedance. This structural incompatibility leads to reflected signals, reduced energy transfer, and potential damage. In calibration terms, mismatch blocks the very conditions necessary for alignment. The system cannot absorb or respond to the input energy in a predictable or linear fashion.
Practical examples abound:
In electrical transmission lines, a mismatch between the source and load results in standing waves and power reflection. In audio systems, using speakers with incorrect impedance ratings leads to distortion, overheating, or amplifier failure. In antenna systems, mismatch between the feedline and the antenna causes signal reflections and degraded transmission quality. In each case, the energy exists – the source is active – but due to structural incompatibility, the intended recipient cannot utilize the energy. This creates a break in the system’s logic loop and introduces instability.
The Bounce-Back Effect: Reversal Through Rejection
When a signal encounters a system that cannot absorb or process it due to mismatch, it is reflected – sent back toward the source. This is not passive rejection; it is active reversal. The initiating system may have invested energy, but that energy fails to transfer, and in returning, it destabilizes the source itself.
Consequences include:
- Signal noise and oscillation, where the reflected energy creates interference in the original circuit.
- Distorted readings, as the measurement apparatus misinterprets echo patterns.
- Overload or thermal stress, particularly in sensitive emitters that are not designed to absorb returned energy.
- Feedback loop corruption, where repeated bounce-back events degrade the source’s calibration reference points.
- The signal appears active, but no actual transmission is taking place. All energy is locked in reversal.
This is where calibration tools reach their limit. Oscilloscopes may detect the bounce. VNAs may quantify the mismatch. But no tool can resolve a mismatch between fundamentally incompatible systems. The impedance mismatch represents a hard boundary – one that is not subject to fine-tuning, duplicity, or workaround.
Why Forced Calibration Cannot Overcome Mismatch
Calibration assumes that alignment is possible – that the system has the capacity to respond predictably to known input. Impedance mismatch violates this assumption at a structural level. No matter how refined the calibration protocol, or how sophisticated the measurement device, you cannot force compatibility where it does not exist.
Attempts to do so result in:
- Measurement error: readings that misrepresent true energy flow.
- Energetic rejection: the system actively resists the imposed calibration.
- System failure: prolonged exposure to mismatch leads to instability, degradation, or shutdown.
Consequences of Mismatch in Energy Systems
Reduced Power Transfer: The system receives only a fraction of intended energy, leading to inefficiency or underperformance.
Signal Distortion: Reflected energy interferes with incoming signals, reducing clarity and accuracy.
Equipment Damage: Amplifiers, transmitters, and other source components may overheat or degrade due to repeated bounce-back.
Calibration Drift: Instruments begin to lose alignment as reflection noise distorts their internal baselines.
In essence, mismatch is not a tolerable calibration variable – it is a categorical blocker. Where impedance mismatch exists, recalibration not only fails – it backfires. That backfire does more than destabilize the system. It can produce the exact opposite effect of what was originally intended. An attempt to harmonize becomes a trigger for fragmentation. An effort to align results in total divergence. Instead of connection, you get rejection. Instead of compliance, resistance. Instead of power transfer, overload. This isn’t malfunction – it’s energetic inversion, triggered by structural incompatibility. The more forcefully recalibration is pursued in the presence of a hard mismatch, the more precisely inverted the response becomes.
V. Measuring and Attempting to Calibrate Mismatch
In the realm of electrical and RF systems, diagnosing impedance mismatch begins with high-precision instruments and calibration techniques designed to isolate, quantify, and account for deviations – set against approved benchmarks. However, even the most refined measurement setups have limitations. While these tools can detect and correct known errors, they cannot rewrite the fundamental architecture of a mismatched system. Diagnosis can expose incompatibility; but it cannot force alignment.
- Tools and Techniques for Diagnosis. The primary tool for detecting mismatch in RF and microwave systems is the Vector Network Analyzer (VNA). This device measures scattering parameters (S-parameters); specifically, how energy is reflected or transmitted at various frequencies. VNAs can analyze both the magnitude and phase of reflections, offering a detailed map of how a device under test (DUT) responds to input signals. To ensure accuracy, VNAs require careful calibration using Open, Short, and Load (OSL) standards. These provide reference impedance states that define the system’s calibration plane. By establishing a known baseline, the analyzer can subtract out errors introduced by the measurement setup itself; such as cable losses, connector mismatches, or phase delays. Common calibration procedures include: – Thru Calibration: Aligns the VNA across two ports by directly connecting them, compensating for path losses and mismatch. – Open/Short/Load Calibration: Ensures the instrument understands how ideal reflective and absorptive conditions behave at the reference plane.
- Reflection and Reversal: The Persistence of Structural Incompatibility. Even with a perfectly calibrated VNA and an ideal testing environment, reflections still occur if the DUT has an inherent impedance mismatch. These reflections aren’t due to instrumentation error – they’re caused by architectural incompatibility embedded in the DUT’s design or material composition. The system may detect and display the mismatch clearly. It may even apply correction factors or modeling techniques. But it cannot compel a calibration where the device’s impedance fundamentally diverges from the system’s. The result is:
- Residual error that cannot be eliminated
- Loss of signal integrity across the interface
- Energetic rejection that mirrors the mismatch back to the source
- Calibration tools correct known, modeled imperfections – not structural incompatibility.
3. Techniques That Reveal Incompatibility. Several diagnostic approaches are used to identify hard mismatches:
Reflection Method: Measures the reflection coefficient (Γ), directly quantifying how much input signal is bounced back rather than absorbed.
Series Through and Shunt Through Methods: Insert a known impedance in series or parallel with the DUT and observe how it alters circuit behavior. Significant phase or amplitude shifts signal mismatch.
These methods don’t resolve the mismatch – they verify that it exists, and to what extent.
4. Real-World Factors That Compound Mismatch
Poor Connectors or Cables: Even minor defects in the physical interface can create localized mismatches that propagate through the system.
Environmental Drift: Changes in temperature, humidity, or mechanical stress subtly alter component impedance over time.
Frequency Sensitivity: Higher frequency systems are more susceptible to reflection, making mismatch effects more severe.
Uncertainty Analysis: In high-precision environments, small variances compound. Quantifying uncertainty is essential for understanding measurement boundaries.
Closing Point
No matter how advanced the calibration process, tools, or modelling techniques – if the component’s core characteristics diverge from the system’s impedance, true calibration is impossible. The outcome is predictable. The signal is rejected. The energy reflects. The source may shut down – not from a failure of effort, but from fundamental incompatibility. This is the boomerang effect made real: not a metaphor, but an engineering truth. Where energy cannot be absorbed, it returns – with force, with distortion, and with consequences. Now we are all clear on the “can and can’t” of real calibration, bear in mind those who knows but persisting on the mismatch may just want to deliberately ruin your systems. No pun intended.